
Handloading at the desk? The AMP Press bullet seater can go to the computer, or the computer can go to the loading bench.
The AMP Press bullet seater is completely different and far advanced beyond any other reloading press you’ve ever bolted to your bench, incorporating digital technology to precisely measure case neck tension on a bullet. Consistent case-to-case neck tension is important to keeping groups tight – especially at extended ranges – where a slight difference among cartridges in a batch can widen groups, cause flyers and cost you a championship.
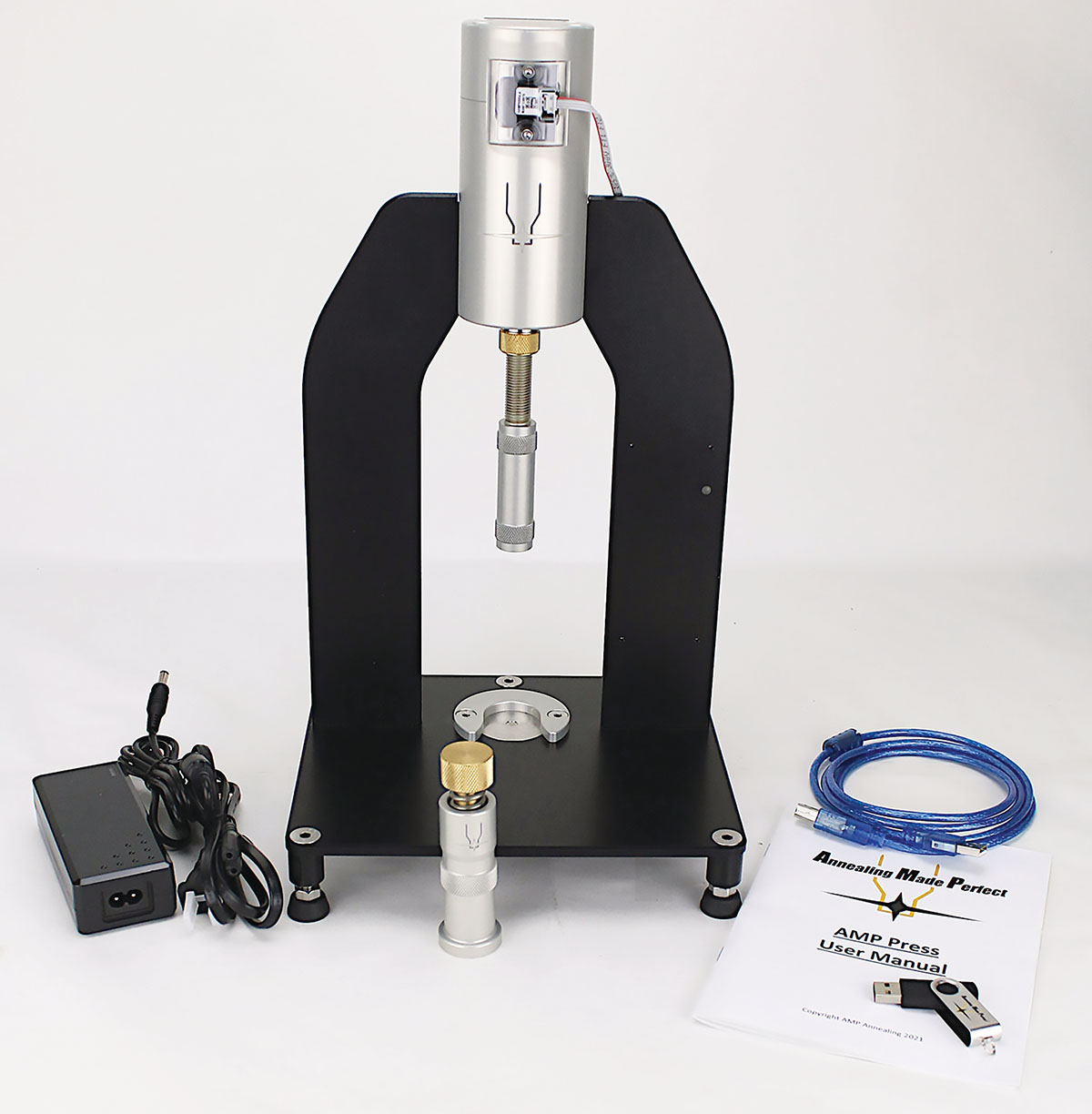
The AMP Press bullet seater comes with everything needed for setup; the software program is downloaded from the AMP website.
New Zealand company AMP (Annealing Made Perfect) designed and manufactures the unique AMP Press bullet seater, the heart of which is a load cell. AMP’s load cell press is a kind of spinoff from the company’s flameless cartridge case annealing machine, the AMP Annealer, that heats via induction – similar to a kitchen induction stove detailed in
Handloader (No. 346, October-November 2023). A load cell press was necessary for developing the annealer and testing its results. With the AMP Annealer’s success, AMP saw the usefulness of a load cell press to handloaders hounding after the precision part of “precision handloads.”
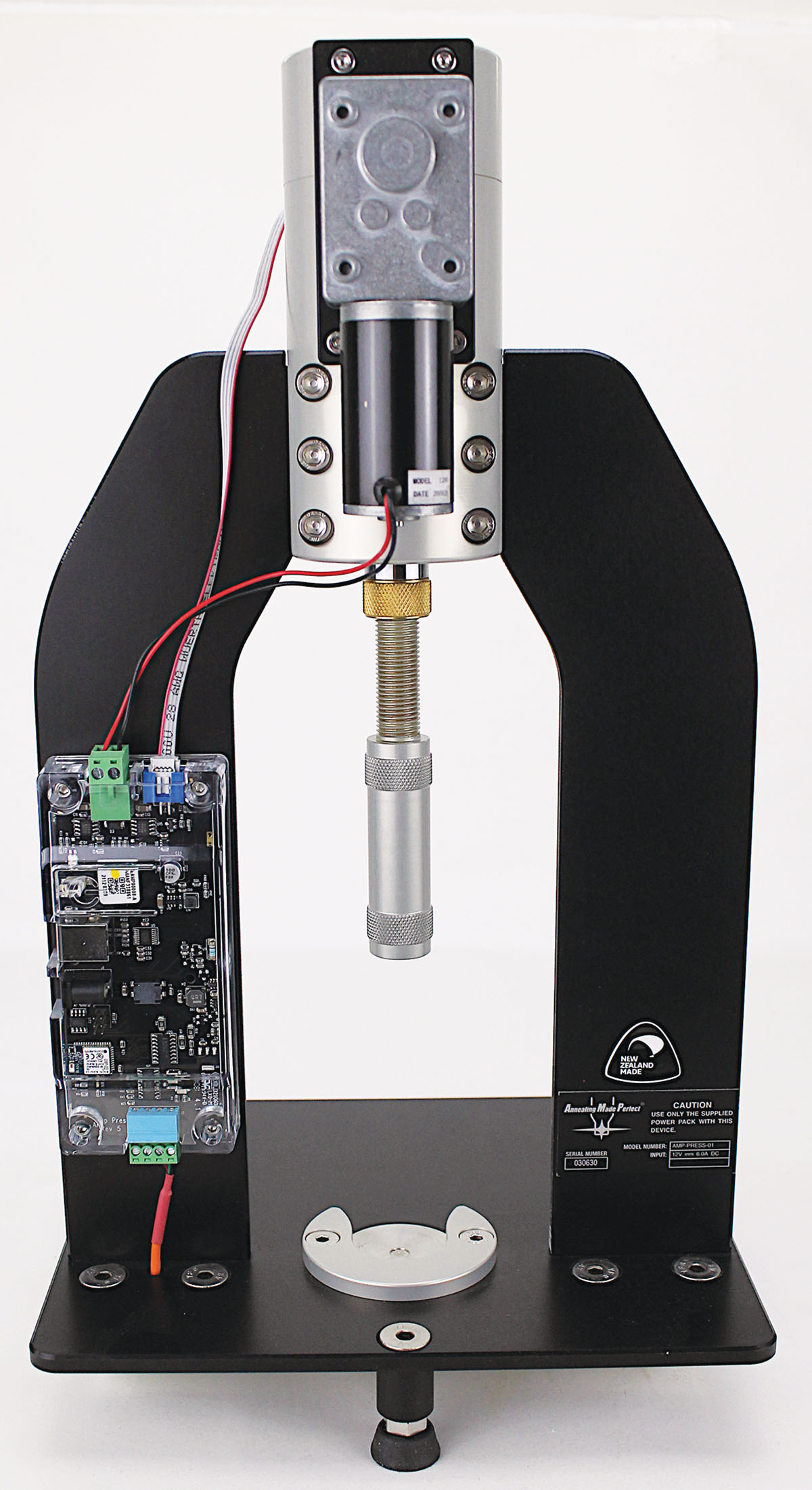
Most of the wiring is at the back of the press, out of the way.
A transducer changes energy from one form to another; a load cell is an electro-mechanical transducer that measures mechanical force or weight and converts it to an electrical output. The AMP Press load cell located at the bottom of the press measures the mechanical force applied to seat a bullet in a case. Connected to a personal computer, it graphs the result on the computer screen, which the user then reads as neck tension on the bullet.
Annealing and neck tension are intimately related. Ammunition manufacturers typically anneal brass between several steps in the case drawing process because each drawing step “work hardens” the brass, and annealing returns brass to a more malleable state – that is, softer, less brittle – and so, easier to manufacture. Handloaders anneal case necks and shoulders because repeatedly firing and reloading brass hardens it, eventually showing up as splits in case mouths, necks, or shoulders. Before that happens, work hardening can cause brass necks to “spring back” away from the resizing die by different amounts, applying differing neck tension on the bullets. This creates variables that may not show up until a precision shooter experiences unexplained flyers and enlarging groups on the target. The case-to-case disparity in the tension the necks apply to the bullets upon seating becomes more and more pronounced from those repeated firings and reloadings unless cases are annealed.
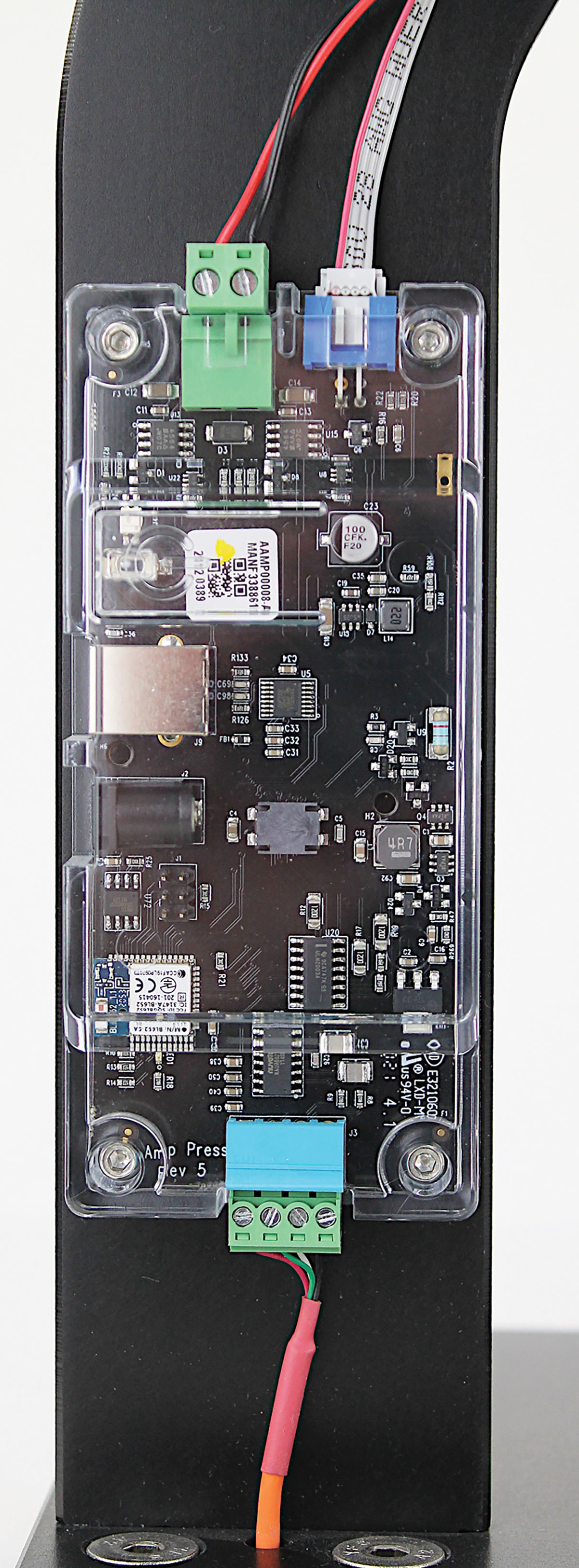
The tidy electronics package is mounted on the back of the press. The lower wiring runs down to the load cell, the upper wiring to the ram motor.
Beyond annealing, the AMP Press can detect other problems, such as a donut forming at the bottom of the case neck, or the anomalous case with a thicker neck. Both of which can cause flyers out of the group on the target. It can alert the user to corrosion or carbon buildup inside a case neck. Because brass from different manufacturers have differing elastic properties, potentially causing a flyer, the press can identify the odd-man-out case during bullet seating. It may also spotlight a case trimmed longer or shorter than the rest. All this comes with understanding how to read the AMP Press program’s computer graphing, which is really a simple X and Y coordinate graph that shows on one axis the force applied to seat the bullet and on the other, the distance the bullet traveled to seat.
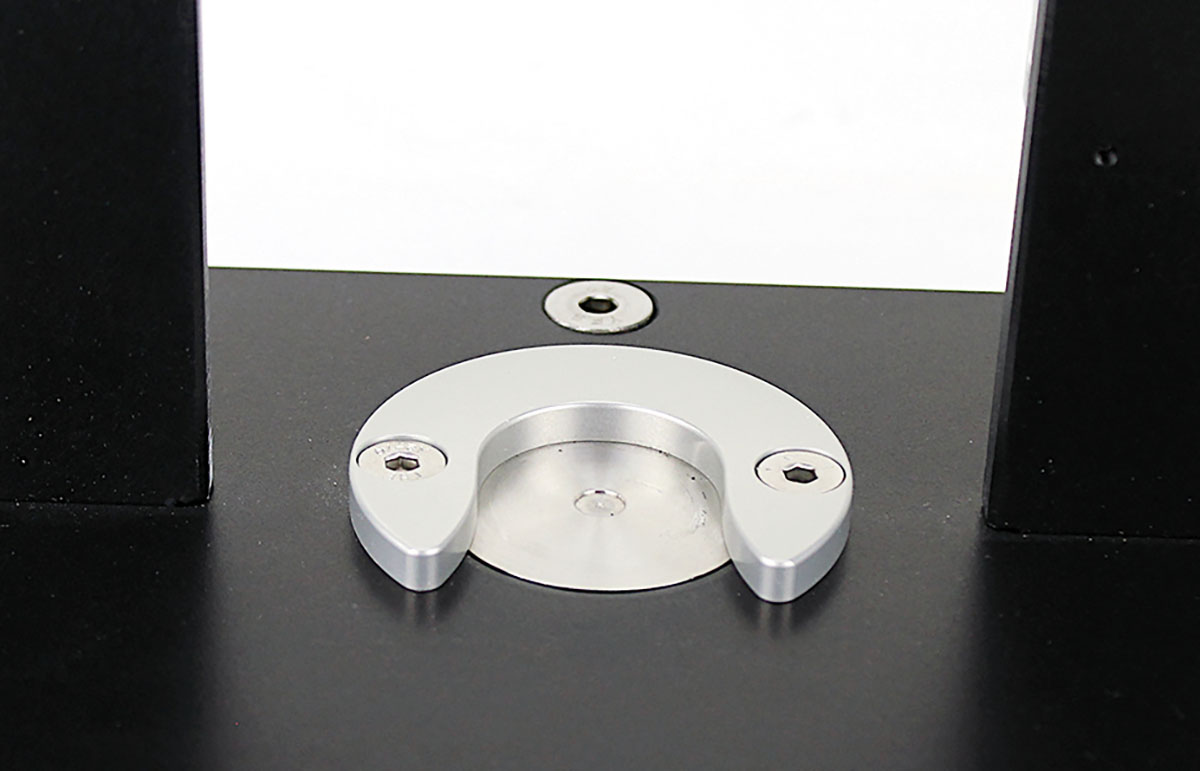
It doesn’t look like much, but the load cell is the heart of the electronic bullet seating press.
Arriving disassembled, the AMP Press is simple to set up; instructions are in the press manual inside the box and on an accompanying flash drive if you prefer video instruction. Even the wrenches and all power and USB cabling are included. The press is 10 pounds of machined steel, with an electric motor mounted overhead to drive the bullet seating ram downward and the electronics package mounted on the back side of the press under a clear plastic cover. The only speedbump I had with the press setup, amusingly enough, was locating the power button, which is somewhat invisible as it is smoothly incorporated into the clear plastic of the cover.
If you’ve ever hooked up a printer to a computer, you can handle connecting the AMP Press. If you don’t want the cabling, it is Bluetooth-compatible. After connecting, retrieve the unlocking key from the flash drive to download the software from the AMP website. The instruction booklet is blessedly thin and concise; only eight pages are needed to describe the graphing, the dropdown tables and how to use the program.
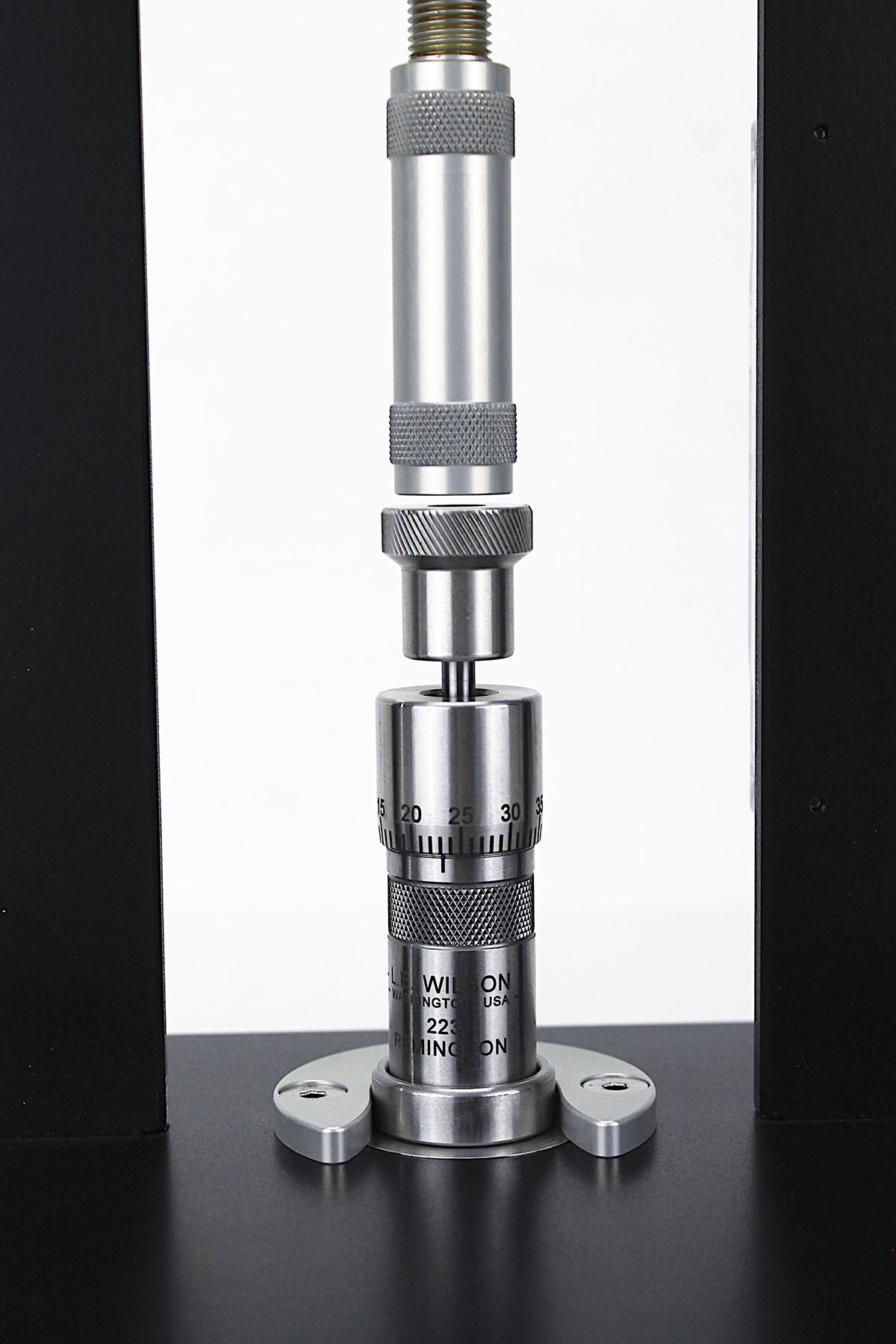
Arbor press dies, such as the Wilson nestled in its cup, are required for bullet seating. Here, the press ram is poised above the die’s seating stem.
AMP thoughtfully includes a spring-loaded “simulation die” so that the first-time user can get into the learning curve without needing to sacrifice any match-tuned cases. There is also a learning curve, as with any software program. The AMP Press program isn’t a thousandth as complex as all the app chaff in a smartphone, and I was able to get up to speed on the features in the first session, though a refresher might be in order after not using the AMP for an extended period. The simulation die will be handy again for that.
This is an arbor press, so standard 7⁄8x14 threaded dies aren’t going to work; instead, Wilson Micrometer Top Bullet Seating dies are the way to go. Bullet seating is the only operation the AMP Press performs; a standard reloading press is still needed for case resizing and other operations.
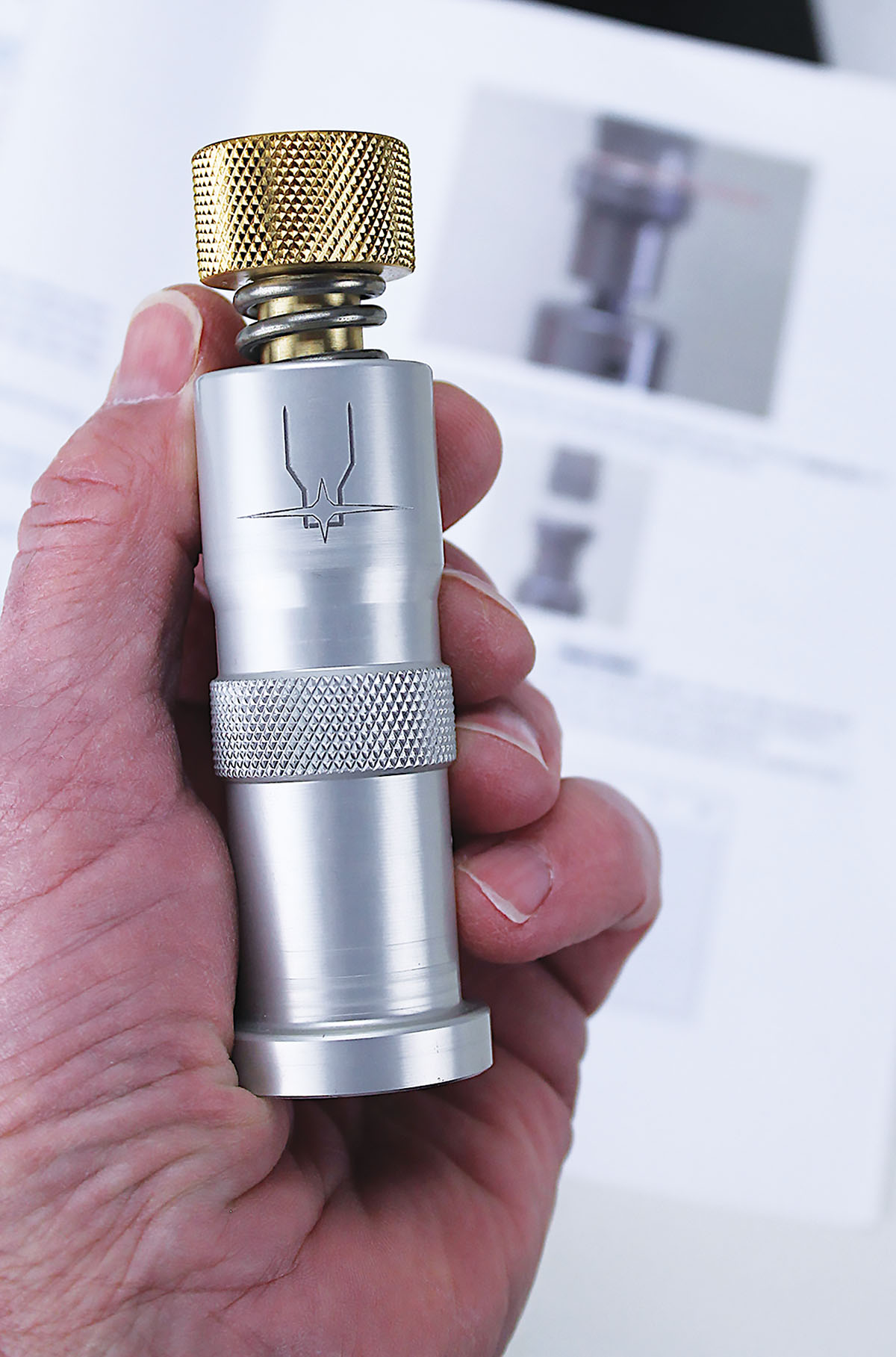
A “simulation die” is included for learning how to use the press and program without sacrificing brass cases.
Once the seating die is adjusted for the desired seating depth and the die adjusted to the press, a bullet goes on the case, the case goes in the die, the die (and its bottom cup) go onto the load cell. Click “GO” on the computer screen and the ram drives downward to seat the bullet. The ram moves at about the same speed as when carefully seating a bullet on any hand-operated press, and the sensor is accurate to within +/- .001 inch. The program immediately displays the graph on the computer screen for your satisfaction or consternation with your case prep job and troubleshooting problems you would otherwise not have detected. The graphs can be labeled and saved as PDF documents for future reference.
For evaluation here, after some self-education and training with the instruction booklet and simulation die, I utilized two batches of 5.56 NATO Lake City (96) brass and 69-grain Sierra MatchKing bullets to see whether the AMP Press would indicate the difference in neck tension between annealed and unannealed cases. All cases in both batches have been reloaded five times (for High Power competition shooting). One batch has never been annealed, and the second batch was annealed with the AMP Annealer before seating bullets. After cleaning, all cases passed through a Hornady Custom Grade full-length resizing die and then a Wilson case trimmer to a uniform 1.750 inch. I measured neck wall thickness to ensure a variation of not more than +/- 0.002 inch.
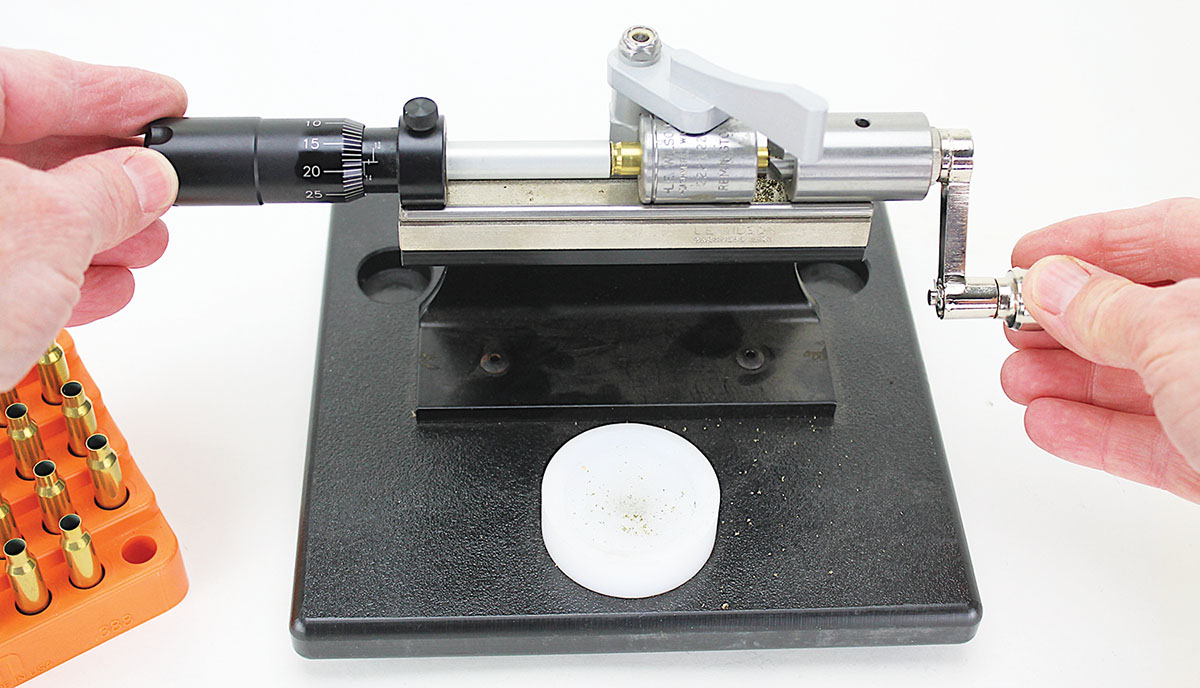
The test cases were carefully trimmed, but the AMP press detected one case that was .001 inch longer than the others.
An accompanying photo clearly shows how the AMP Press graphed the similar bullet seating force for three annealed cases (blue traces) and then singled out the fourth, unannealed case as a glaringly obvious anomaly (red trace). The vertical (Y) axis of the graph indicates the three annealed cases required 110 to 120 inch-pounds of peak force to seat bullets, whereas the unannealed case needed only 80 inch-pounds. The latter unannealed case, then, is gripping the bullet with significantly less tension than the annealed cases – a potential flyer. “The reason for this is that the unannealed case still has spring back out of the sizing die, resulting in less neck tension during seating,” Alex Findlay explained in an email exchange when I showed him the image of the graph. Alex is the AMP Director and has been closely involved in developing both the AMP Annealer and AMP Press.
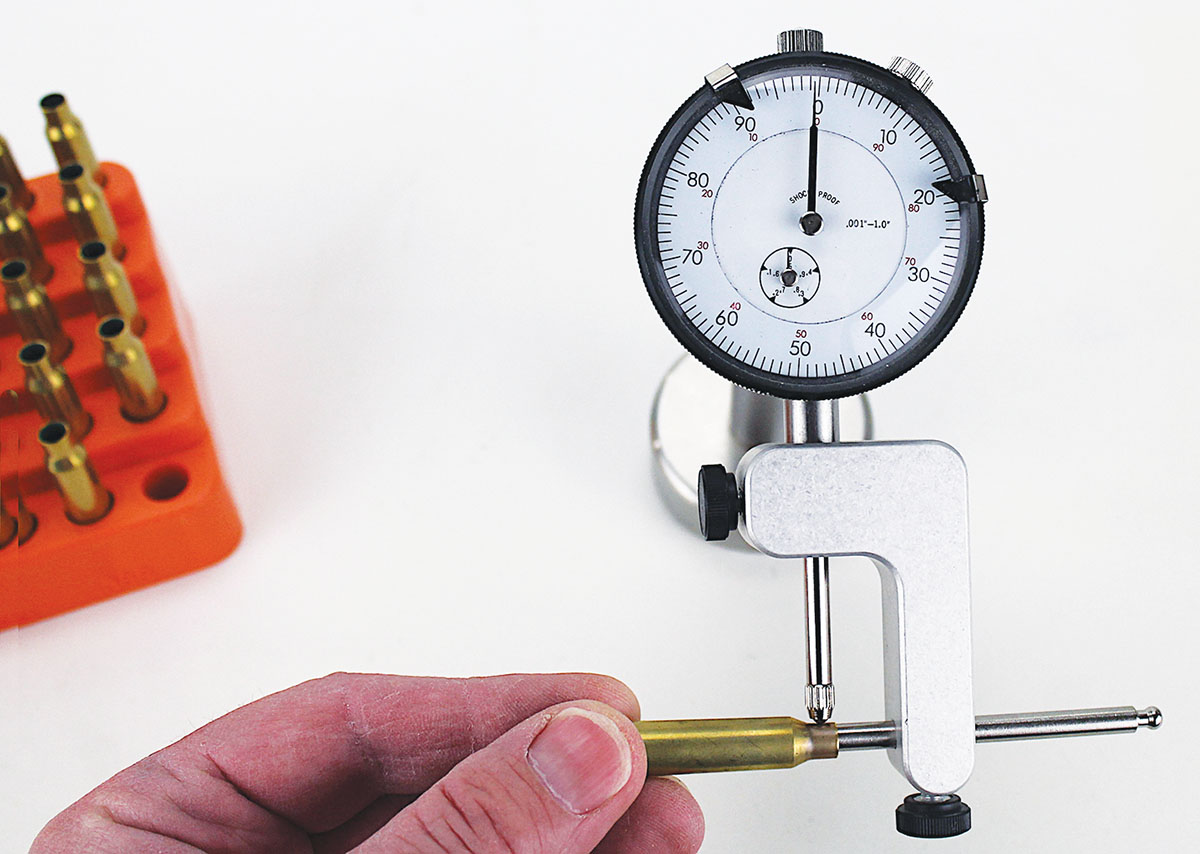
Test cases were culled for +/- .002-inch neck thickness.
Reading the horizontal (X) axis
from right to left in the photo shows three of the bullets traveled about .0265 inch to seat, and the fourth – the first blue line to rise vertically – traveled about .0275 to seat. Because the latter bullet traveled .001 inch in further contact with the case when seating, it indicates that the case was trimmed about .001 inch longer than the other three, or that perhaps the case chamfer varied from the other two, or that the bullet is a tad longer than the others. (The short, flat line of all four traces starting from the left is the “zero loading” distance, the distance the ram traveled before contacting the die’s seating stem.)
All three annealed cases (blue traces) show good uniformity. At the “0.10” point on the horizontal (X) axis, the force required to seat those bullets drops off dramatically from 110-120 inch-pounds to about 46-49 inch-pounds of “terminal force,” indicating the bullet bases have passed the case neck/shoulder junctions. The unannealed case (red trace), however, continues to resist bullet seating beyond that same point, still requiring about 72 inch-pounds of terminal force to seat. (Terminal force is also spelled out in the table to the right of the graph in the photo below.)
“This is again due to spring back, but with the opposite effect,” Alex said. “When the bullets were fully seated in the annealed cases, the necks tended to conform to the new dimension created by the bullet. Therefore, the force dropped off after the bullet had passed all the way down the neck. The unannealed neck, however, tried to retain its dimension, creating more seating force past the neck/shoulder junction. I have just done a quick test in the lab to confirm this.”
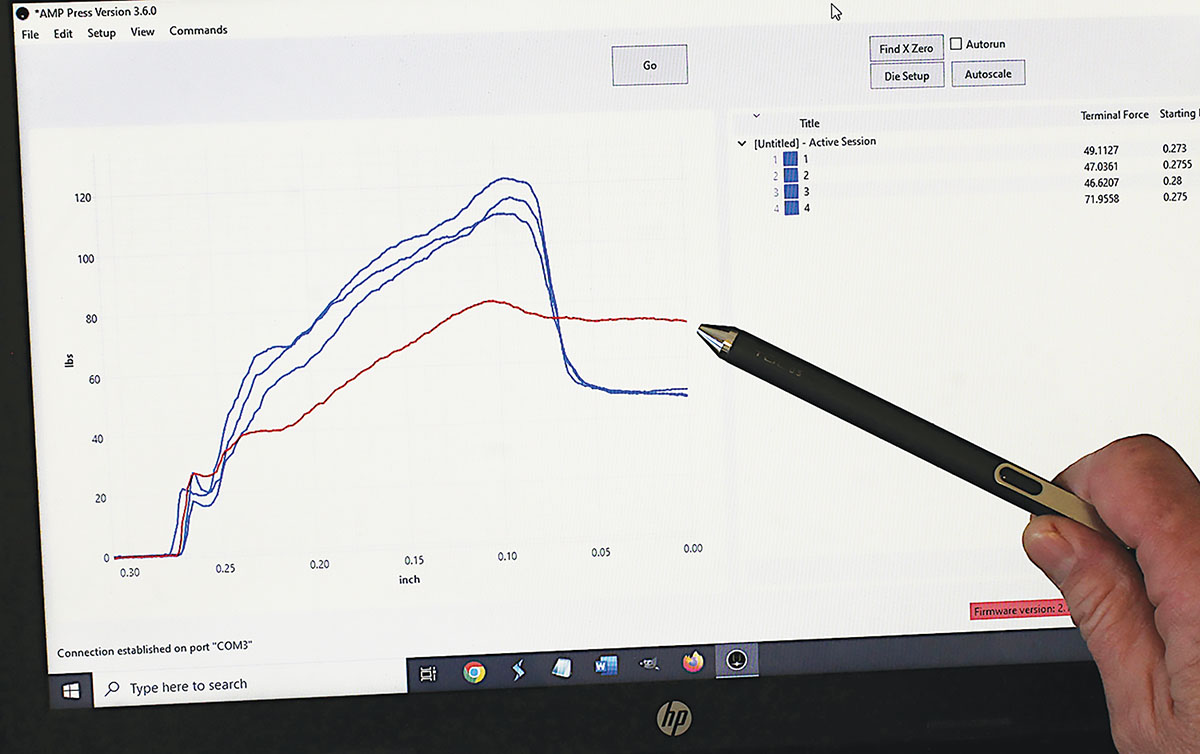
The red trace on the graph pinpoints the unannealed case as having significantly less neck tension than the annealed cases (blue traces).
Retailing for $1,395 (available at AmpAnnealing.com/amp-press/), the AMP Press is the first tool to show the handloader graphically and precisely what’s happening with neck tension, and it illustrates for us the direction precision handloading has been taking, the interfacing or incorporation of digital technology into precision mechanical technology. We saw it first in our chronographs, a much-needed development because no accurate mechanical measurement of bullet velocity could be made in a simple, affordable, and readily transportable package for Joe Average Handloader. Chronograph technology itself evolved from vacuum tubes and bullets punching sensitized paper to optical detection of bullets to today’s Doppler radar units. Powder scales, too, went digital and then incorporated automatic tricklers, as well – another example of utilizing load cell transducer technology.
Here we have the first successful application of digital technology to Joe’s reloading press operation, limited to bullet seating for now (though perhaps “limited” is unfair). Despite my opening comment, the AMP Press doesn’t actually bolt to the reloading bench; rather, it sits there on its own sturdy legs, awaiting work like a placid Sphinx or maybe like an AA/Fuel dragster anticipating the green light into the future. What’s next?
I vote for a compact, affordable digital strain gauge that attaches easily onto the exterior of a rifle chamber to precisely measure chamber pressure. Someone is hopefully working on that now.